CNC Grinding Machine: The Future of Precision Grinding
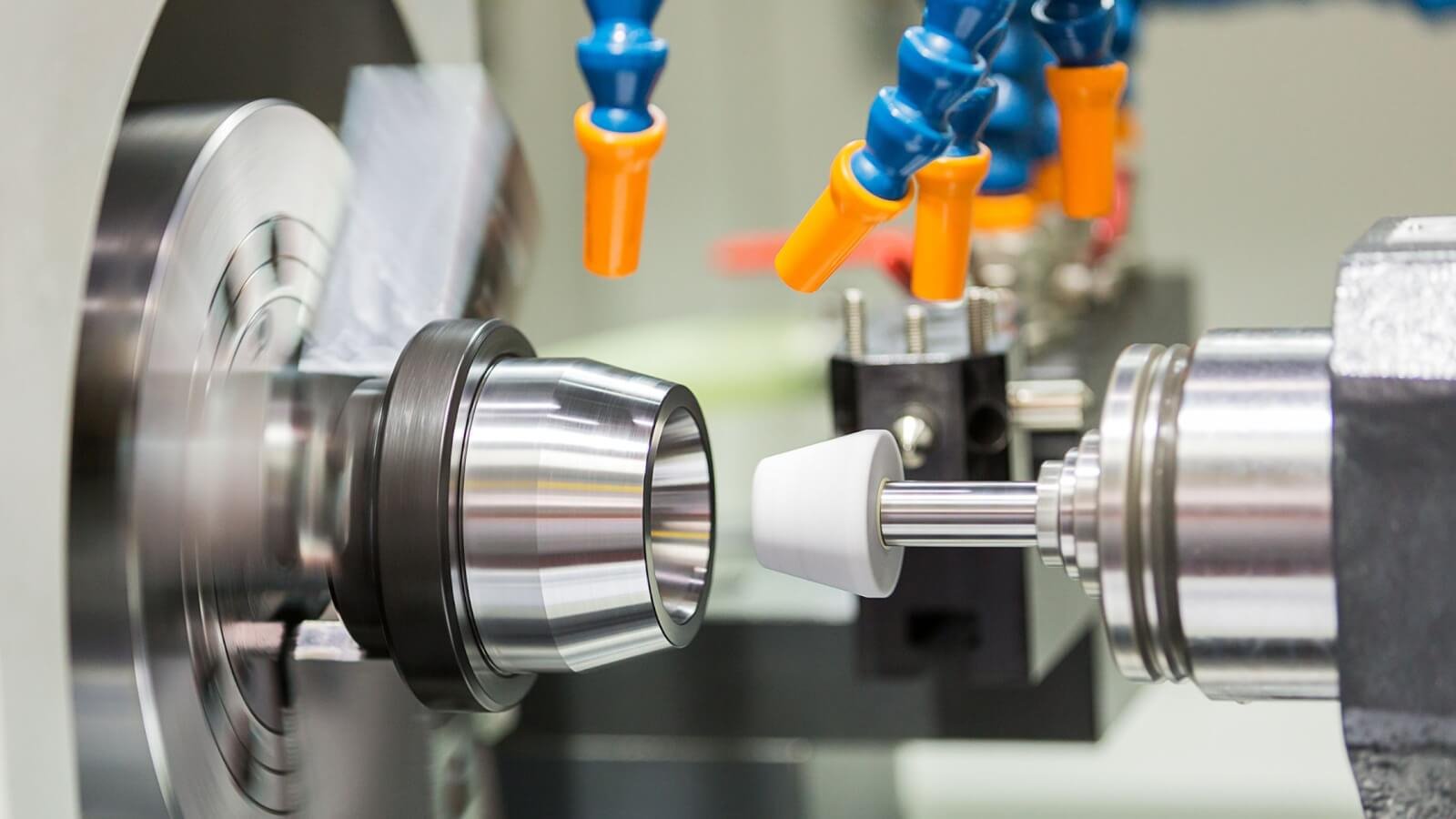
Introduction to CNC Grinding Machines
CNC grinding machines are at the heart of modern manufacturing, delivering unmatched precision and efficiency. With the ability to perform intricate material removal processes, these machines are widely used in industries like automotive, aerospace, medical, and electronics. The significant advantage of CNC grinding machines lies in their automation, which allows for high-precision components to be produced in an efficient and consistent manner.
In this article, we will explore the functions, types, advantages, and applications of CNC grinding machines, highlighting how they are transforming industries by providing highly accurate grinding solutions.
What is a CNC Grinding Machine?
A CNC grinding machine is an advanced tool used for grinding surfaces, internal diameters, external diameters, and complex shapes on metal or other materials. The term “CNC” stands for Computer Numerical Control, meaning that these machines are operated using a computer program rather than manual controls. This automation enables CNC grinding machines to execute precise grinding operations with little human intervention, reducing the risk of error and ensuring consistent quality.
These machines use rotating grinding wheels or other abrasive tools to remove material from a workpiece. Depending on the design and function of the machine, it can handle a range of grinding applications, from shaping complex components to finishing delicate parts with a smooth surface.
How CNC Grinding Machines Work
CNC grinding machines operate on the same basic principle as traditional grinding machines, but with a much higher level of precision and automation. The process starts by placing the workpiece onto the machine, where it is securely fixed. The machine then uses a rotating grinding wheel that moves in predetermined patterns to remove material from the workpiece, shaping it to exact specifications.
The key feature of CNC grinding machines is their control system, which is computer-driven. The operator inputs the desired parameters into the CNC system, which automatically adjusts the grinding wheel’s position, speed, and pressure to ensure optimal results. With this control system, CNC grinding machines can achieve extremely tight tolerances (up to a few microns), making them ideal for industries where precision is paramount.
Types of CNC Grinding Machines
CNC grinding machines come in various types, each suited to specific grinding operations. Some of the most common types include:
-
CNC Surface Grinding Machines
CNC surface grinding machines are used for producing a flat surface on a workpiece. The grinding wheel moves over the surface of the part to remove material, ensuring a smooth and even finish. These machines are commonly used for finishing metal parts, creating components with fine tolerances and high-quality finishes. -
CNC Cylindrical Grinding Machines
CNC cylindrical grinders are designed to grind the outer and inner diameters of cylindrical workpieces. This type of machine is used to produce precision components such as shafts, spindles, and other cylindrical parts. The grinding wheel rotates against the workpiece, removing material while maintaining tight dimensional accuracy. -
CNC Internal Grinding Machines
CNC internal grinding machines focus on grinding the inner surfaces of a workpiece, such as bore holes. This type of grinding machine is ideal for producing smooth, accurate inner diameters in components used for automotive, aerospace, and tooling applications. -
CNC Tool and Cutter Grinding Machines
These machines are specifically designed to sharpen and recondition cutting tools. CNC tool grinders are essential for industries that require precise cutting tools, such as milling cutters, drills, and end mills. They allow manufacturers to restore the sharpness of tools and extend their life, improving overall productivity. -
CNC Jig Grinding Machines
Jig grinders are used for precision finishing of hard-to-machine parts, such as precision holes, slots, and surfaces. The high accuracy offered by CNC jig grinding machines makes them ideal for mold making, tooling, and other applications requiring tight tolerances and fine finishes.
Benefits of CNC Grinding Machines
CNC grinding machines offer numerous advantages that have made them indispensable in modern manufacturing processes. Some of the most notable benefits include:
-
Unmatched Precision
One of the key advantages of CNC grinding machines is their ability to achieve high precision. CNC technology allows for extremely fine adjustments, which results in components with very tight tolerances. Parts can be produced with accuracies up to 0.0001 inches (0.0025 mm), making CNC grinders essential for industries requiring exceptional accuracy. -
Increased Efficiency
With the automation provided by CNC systems, these grinding machines can operate without constant supervision, reducing the need for manual adjustments. This leads to faster production times and reduced cycle times. CNC machines can also perform grinding operations continuously, minimizing downtime and increasing productivity. -
Consistency and Repeatability
CNC grinding machines are designed for repeatability, meaning the same part can be manufactured multiple times with identical results. This consistency is critical in industries like automotive and aerospace, where the reliability and performance of components must be ensured in every unit produced. -
Complex Geometry Capability
CNC grinders are capable of grinding intricate geometries that would be difficult to achieve with traditional manual grinding methods. The CNC control system allows for precise movement in multiple directions, enabling the creation of complex shapes, profiles, and surface finishes. -
Reduced Human Error
By automating the grinding process, CNC grinding machines minimize the risk of human error. The computer-controlled system ensures that the grinding wheel operates with optimal speed, pressure, and positioning, reducing the likelihood of mistakes that could lead to defective parts. -
Lower Operational Costs
While the initial investment in CNC grinding machines may be higher than traditional grinding machines, the long-term savings are significant. Reduced labor costs, fewer defects, less material waste, and faster production lead to lower overall operational costs for manufacturers.
Applications of CNC Grinding Machines
CNC grinding machines have widespread applications across various industries. Some of the most common uses include:
-
Automotive Industry
In the automotive sector, CNC grinding machines are used for manufacturing precision components like gears, camshafts, crankshafts, and bearings. These components must meet stringent quality standards and perform reliably under high-stress conditions, making CNC grinding an ideal process for their production. -
Aerospace Industry
The aerospace industry relies on CNC grinding machines to produce high-performance components such as turbine blades, landing gear, and engine parts. CNC grinders ensure that these critical components are manufactured to exacting tolerances, which is essential for ensuring safety and reliability in aviation applications. -
Medical Industry
CNC grinding machines are used to produce medical components like surgical instruments, dental implants, and prosthetics. The need for high precision and biocompatibility makes CNC grinding an ideal solution for the medical field. It ensures that parts meet strict regulatory standards while maintaining functionality and safety. -
Tooling Industry
Tool and cutter grinding machines are used to recondition and sharpen cutting tools, such as end mills, drills, and reamers. This process prolongs the life of expensive tooling equipment, enhancing their performance and reducing the need for frequent replacements. -
Electronics Industry
CNC grinding machines are essential for producing precision components in the electronics industry, including connectors, capacitors, and resistors. These parts often require intricate shapes and high-quality finishes, making CNC grinding machines the best option for meeting those requirements. -
Mold and Die Making
In mold and die making, CNC grinding machines are used to create precise molds and dies used in injection molding, stamping, and other manufacturing processes. The precision offered by CNC grinders is crucial for producing high-quality molds that produce accurate and consistent products.
Conclusion
CNC grinding machines have revolutionized the way precision grinding is performed in modern manufacturing. With their high precision, efficiency, and automation, these machines have become indispensable in industries that demand exacting tolerances and quality finishes. Whether in automotive, aerospace, medical, or electronics, CNC grinders are essential for producing components that meet the strictest performance and safety standards.
As technology continues to evolve, CNC grinding machines are likely to become even more advanced, offering enhanced capabilities and greater automation. With their ability to perform complex grinding operations with unmatched accuracy, CNC grinding machines will continue to be a critical part of the manufacturing landscape for years to come.
- التعليم
- Course
- Books
- Drawing
- سؤال
- Film
- Fitness
- Food
- الألعاب
- Gardening
- Health
- الرئيسية
- Literature
- Music
- Networking
- أخرى
- Programming
- Religion
- Shopping
- Sports
- Curriculm
- Wellness